Neuguard's PUWER Services
We provide a wide range of professional services both standardised and taylored to meet your needs.
Provision & Use of Work Equipment (PUWER) Regulations 1998
What is the legal requirement?
The Provision and Use of Work Equipment Regulations 1998 (PUWER) is a set of regulations within the United Kingdom that were established under the Health and Safety at Work Act 1974. PUWER specifically focuses on the health and safety requirements related to work equipment and machinery used in the workplace.
The Health and Safety at Work Act 1974 is a primary piece of legislation in the UK that provides the legal framework for workplace health and safety. It outlines the general duties and responsibilities of employers, employees, and self-employed individuals to ensure the health, safety, and welfare of all persons at work.
PUWER, on the other hand, is a subordinate legislation made under the authority of the Health and Safety at Work Act. Subordinate legislation means that PUWER is a more specific set of regulations that provide detailed requirements and guidance on the safe provision and use of work equipment.
The legal status of PUWER is that it is a statutory instrument, which means it has the force of law and must be followed. It applies to all workplaces and work activities where work equipment is used, except for offshore installations and certain mines. PUWER places legal duties on employers, self-employed individuals, and those who control the use of work equipment, such as equipment owners and suppliers.
Under PUWER, employers and others responsible for work equipment must ensure that it is suitable for its intended use, properly maintained, and used only by competent persons who have received adequate training. PUWER also requires employers to provide information, instruction, and training to employees regarding the safe use of equipment, and to carry out regular inspections and maintenance to ensure the equipment remains safe.
In summary, PUWER is a set of regulations that is legally binding in the UK and is subordinate to the Health and Safety at Work Act 1974. It provides specific requirements for the safe provision and use of work equipment and is enforceable by law. Compliance with both the Health and Safety at Work Act and PUWER is necessary to ensure a safe working environment in relation to work equipment and machinery.
How can employers / users of work equipment comply with the law?
To comply with the Provision and Use of Work Equipment Regulations 1998 (PUWER), employers and users of work equipment can follow these steps:
- Risk Assessment: Conduct a thorough risk assessment of all work equipment in use. Identify any potential hazards and assess the level of risk associated with each piece of equipment.
- Selection and Suitability: Ensure that the work equipment is suitable for its intended use. Consider factors such as the nature of the work, the conditions in which the equipment will be used, and the capabilities of the individuals operating it.
- Maintenance and Inspection: Establish a regular maintenance and inspection regime for all work equipment. Carry out routine inspections to identify any defects or issues that may affect its safe use. Maintain records of maintenance and inspections.
- Training and Competence: Provide adequate training and instruction to employees who operate or use the work equipment. Ensure they are competent and understand the risks associated with the equipment and how to use it safely. Keep records of training provided.
- Information and Instruction: Supply clear and comprehensive information and instructions on the safe use of work equipment. This includes providing operating manuals, warning signs, and safety guidelines.
- Control Measures: Implement appropriate control measures to mitigate risks associated with work equipment. This may include the use of guarding, protective devices, personal protective equipment (PPE), and safe systems of work.
- Emergency Procedures: Develop and communicate emergency procedures in case of equipment failure or accidents. Employees should know how to respond in such situations to minimise harm and prevent further risks.
- Inspections and Testing: Ensure that periodic thorough examinations are conducted for certain types of work equipment. This typically applies to equipment such as lifting equipment, pressure systems, and some machinery. Thorough examinations must be carried out by competent individuals or organisations.
- Documentation and Record Keeping: Keep records of all maintenance, inspections, training, and examinations related to work equipment. These records should be easily accessible and retained for the required duration.
- Review and Continuous Improvement: Regularly review and update risk assessments, control measures, and procedures to adapt to changing circumstances and new equipment. Learn from incidents, near misses, and feedback to continuously improve safety practices.
Why Neuguard?
Compliance with PUWER requires a proactive approach to ensure that work equipment is safe for use, employees are trained and informed, and appropriate measures are in place to minimise risks. It is important to consult the full text of the regulations and seek professional advice when necessary to ensure full compliance with PUWER requirements.
It is precisely in this area that Neuguard can assist your business as a competent consultancy partner for PUWER compliance.
Please contact us today if there is anything we can do to assist you with your project.
Ensure Safety
Ensure Compliance
Reduce Downtime
Reduce Costs
How do we work?
We will come to your site and perform physical assessments of the equipment under the applicable PUWER Regulations.
Neuguard have the capability of performing assessments on multiple assets from simple hand tools in a workshop to factory wide machinery.
After the assessment has been completed, a report will be issued detailing all hazards/non-compliances with clearly described and illustrated remedial action recommendations to bring the equipment back into compliance.
First a checklist will be filled out identifying where the equipment either complies, does not comply or is not applicable to the regulations. Then, for each non-compliance, a risk evaluation will be performed detailing the hazard identified, the risk scores associated with the hazard and recommendations for corrective action (an example of a Neuguard checklist and risk evaluation are shown).
Neuguard offers an optional service for sign-off following the completion of the corrective actions. This may be performed in person or remotely.ft
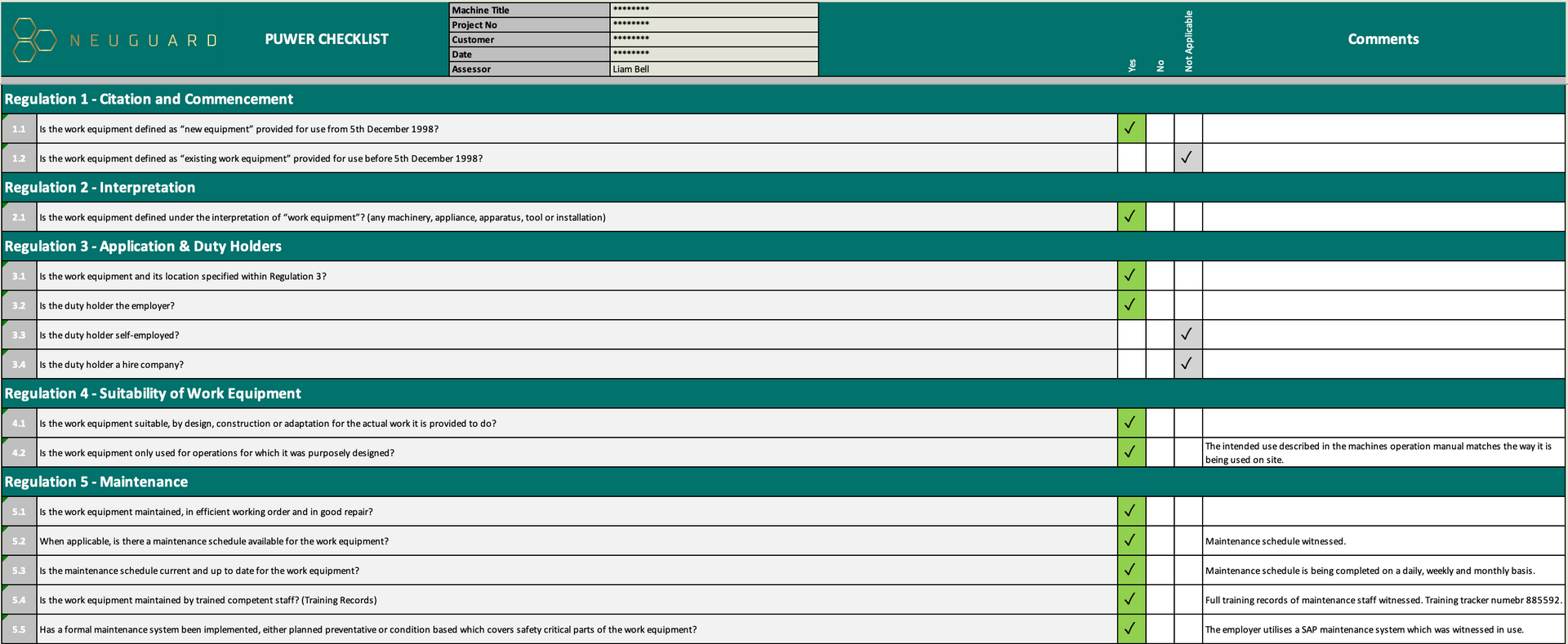
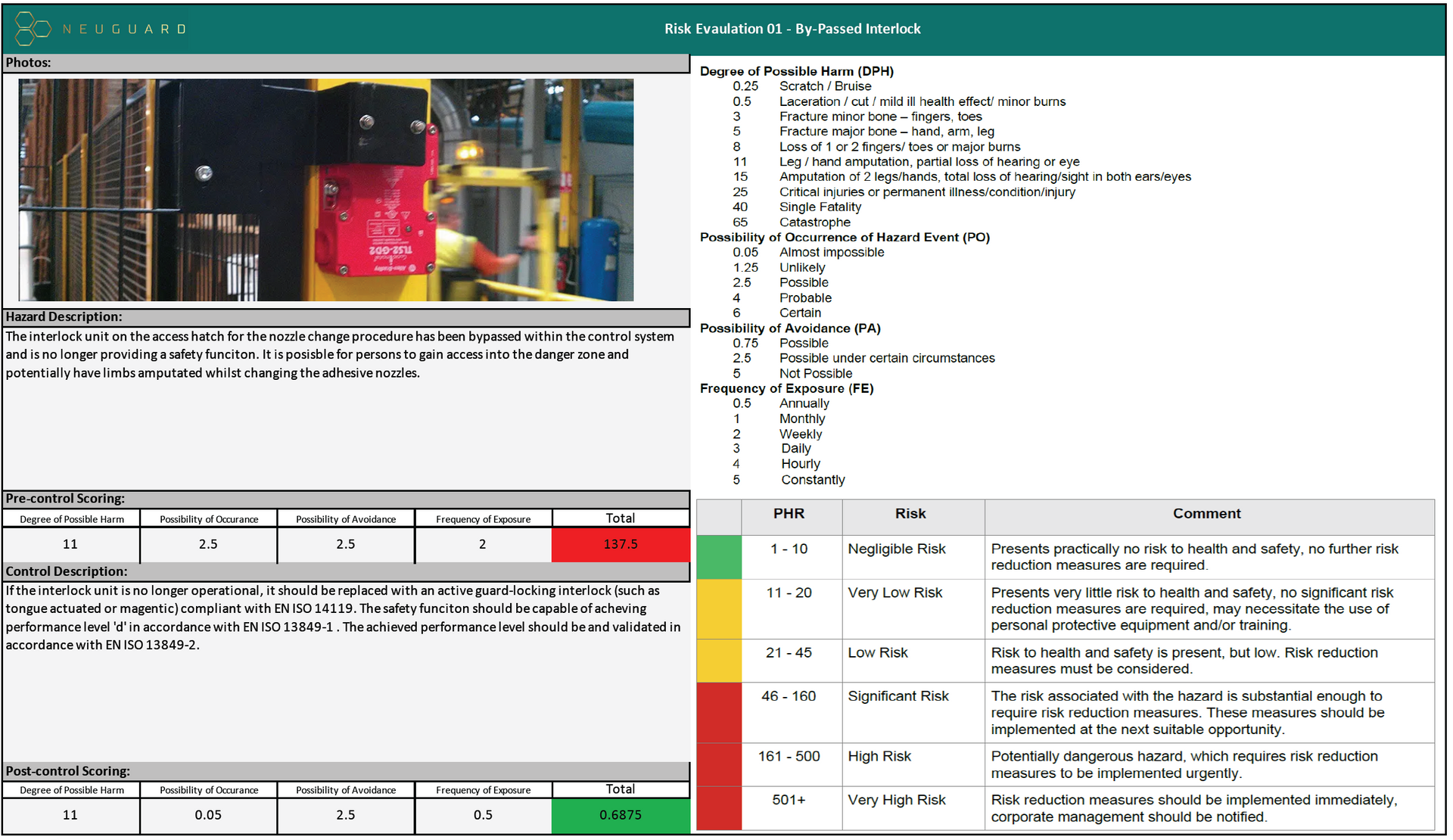